INTERVIEW WITH A COLLEAGUE
Our colleagues talk about their job.
We pursue our series of articles in which we meet the men and women who contribute to the rich tapestry of our company.
Today, let’s meet Céline GOUNON| QSE Manager – Lean Manager|
- Céline, tell us about yourself ? What is your professional background?
QSE Manager – Lean Manager at LJT. I joined the LJT team in October 2013. I used to work in a large heavy metallurgy organization, and my initial training was in QSE. I returned to studying in 2012, at ECAM School of Engineering, where I was awarded a Post-Masters (bac + 6) degree in “Lean Management and Continuous Improvement".
- What exactly is the role of QSE Manager – Lean Manager?
Ensuring that our internal and external customers are satisfied while offering an appropriate level of quality. Our markets– and therefore our customers – do not have the same requirement levels. “Over-quality” is just as much of a disadvantage as “non-quality”. As a Lean Manager my role is, above all, that of a coach, to enable the teams to flourish in terms of their autonomy in a comfortable and effective working environment.
- Which are your favorite aspects of your job?
Relations with others. I have a cross-functional role that allows me to work with all interested parties : internal players (management, operators, support services, Tunisian site),and external players : customers and suppliers as well as other bodies such as healthcare and safety services (e.g. occupational medicine, local authorities).
- Can you describe your working day in 3 points?
The operating standard for production has very recently become 3x8.
1- When I arrive, I work my way around the company’s various departments to greet the teams and to find out if everything is going well. I do the same thing for the teams in the afternoon.
2- I lead the production meeting (UAP) at 9 am every morning. After these two rituals, my schedule for the day is finalized.
3- In the mornings I tend to focus on work in the field, and in the afternoons I tend to work more on formalizing standards, resolving problems, indicators and miscellaneous customer documentation.
- Which project(s) have you particularly enjoyed working on?
All projects at Joint Technique are exhilarating, but one of the most memorable was the “cutting/machining” one.
This project took a year for the industrialization phase. For me, it was a huge playground where I was able to set up the Kanban, define the operating and quality standards, train the teams and, above all, work very closely with the customer in a win/win partnership.
This project is currently a pilot project for the rest of the company.One of my ongoing tasks for this year is to improve the performance of the UAPs with complete autonomy and well-being in the work.
This sort of project can reveal previously hidden skills amongst our colleagues.
- What training would you like to do next? And which conference/professional event would you like to attend next?
“Elence” is a regional program that places humans at the heart of the company’s global performance by working on health, safety and motivation issues. This is a brand new program that is dear to our heart because it will enable us and all of our teams to grow..
LJT is one of the pilot companies in this respect.
- Do you like working at LJT? And can you tell us why?
I find the work at LJT really enjoyable: There is trust at every single level. Team spirit and people’s willingness to listen are rare assets that are firmly entrenched in our company culture. This means we can do great things and rise to challenges that few other companies can do so flexibly.
What has allowed me to flourish is the support and the increase in the teams' skills in terms of QSE and our continuous improvement.
My satisfaction is linked to the company’s performance (quality level, customer service rates and results of colleagues’ individual interviews).
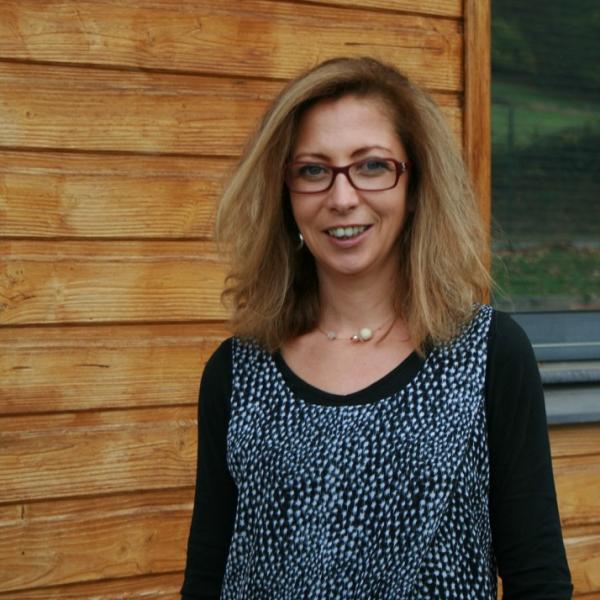