First silicone 3D printing solutions
3D printing is a technology that is still new and evolving.
Not all that long ago, 3D printing was limited to metals (Metal Fusion or Additive Layer Manufacturing (ALM) and thermoplastics (Fused Deposition Modeling (FDM).
Back then, the only solution for flexible materials available to us was a polyurethane FDM – with polyurethane belonging to the large family of thermoplastics – but there was nothing for vulcanized elastomers.
The drawback of polyurethane is that it has very limited mechanical and thermal characteristics (low elastic recovery, poor temperature behavior and low compression set).
But now, thanks to the support of its Liquid Silicone Rubber (LSR) suppliers and the latest developments in these materials, LE JOINT TECHNIQUE can offer you a new silicone 3D printing technology: Drop on Demand.
This is a solution for rapid prototyping or very small series of silicone parts.It produces parts that are very realistic, both geometrically and mechanically; only the external appearance of the part differs, since graining or polishing is, of course, not possible.
With silicone 3D printing, the mechanical characteristics are almost identical to those of a molded part made from LSR. The temperature behavior is very similar to that of conventional silicones (>200°C).
This technology is already offered in several hardnesses, and even color can be added! :
- 20 Shore A : skin (Pantone 7513C), RAL 9011 Graphite Black, RAL 3000 Flame Red, RAL 9010 Pure White, RAL 5010 Gentian blue and RAL 7001 Silver Gray
- 30 Shore A, 40 Shore A and 60 shore A : Translucent, RAL 5010 Gentian blue, skin (Pantone 7513C), RAL 9011 Graphite Black, RAL 3000 Flame Red, RAL 9010 Pure White and RAL 7001 Silver Gray
It will soon become an indispensable milestone for your developments because silicone 3D printing enables you to confirm the ease of assembly and functionality of your parts very quickly and at a lower cost.
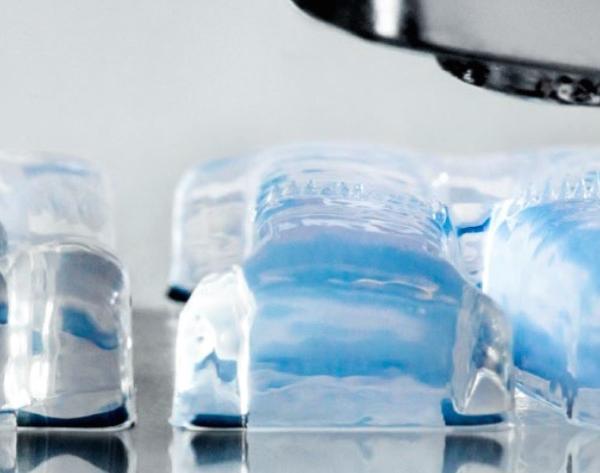